Building True Resiliency in Manufacturing
Business resiliency can be defined as the ability to absorb an unpredictable shock that could harm the organization. Such unpleasant surprises could include a pandemic, a financial crisis, volatile commodity prices, or disrupted logistics chains.
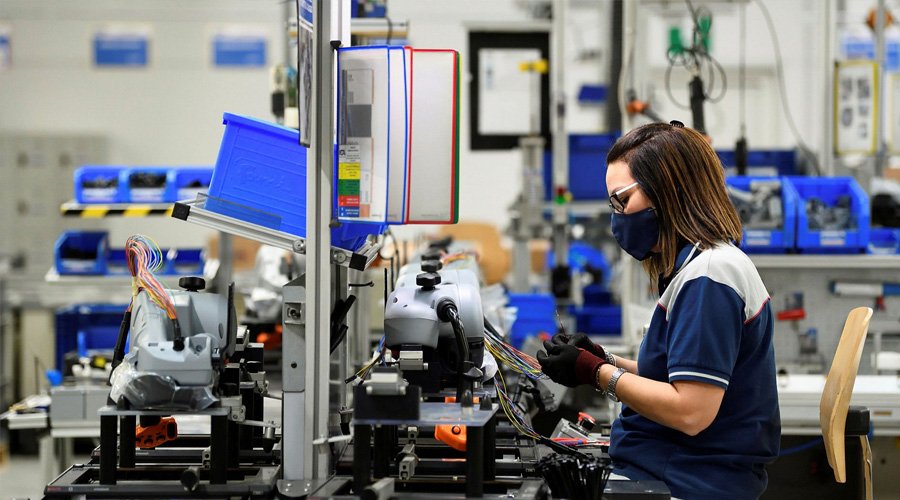
Today, there are just too many unpredictables that can cause sleepless nights for CEOs. We have reached the limits of traditional management approaches based on risk prediction and mitigation.
Let us be frank: There is no real “new normal” coming soon. The world is instead heading into a post-vaccination period characterized by extreme uncertainty. Local situations are impacting global business. Countries are becoming more protective when it comes to the health of their citizens and business interests.
There are other concerns as well. Mutual trust, for example, is ideal — but clients will quickly abandon a supplier if they can get better service at a better price. Cyberattacks also remain a distressing threat. Such attacks in manufacturing have risen 300% during the pandemic as hackers have taken advantage of remote work setups, according to the NTT 2021 Global Threat Intelligence Report.
How to Achieve True Resilience in Manufacturing
When I discuss the resiliency concept with manufacturers that are seeing supply chain troubles or plunging demand, managers are apt to reply: “But we spotted the risk too late and there’s no time to solve it properly. We need to do something right now!”
Building resilience requires strategic thinking. A “rescue net” must be created that enables the business to absorb disruptions without dragging operations to a halt. This involves more than just cherry-picking use cases. For some solutions and approaches, there may be no short-term ROI. Not all risks can be identified and mediated immediately.
The Role of Digital Technology
Organizations, obviously, have different levels of digital maturity. However, IDC research has found that just 30% of manufacturing organizations worldwide describe their digital strategies as “integrated” — and just 11% describe them as “transformative.”
Think about that: Almost 60% of manufacturing organizations admit they are not fully utilizing the potential of digital technology!
Let us recall the three pillars necessary to achieve true resilience:
- Organizational setup
- Adjusted processes
- Technology backbone
What Have We Learned in the Last 18 Months?
First, aligning business strategy with digital development is crucial. Every strategic initiative and business investment should have resiliency and sustainable growth principles embedded within them.
A strong and reliable infrastructure, focused on IT and OT security, is also essential. Data must be accessible in real time to stakeholders everywhere. A lot has been written about the benefits of bridging data silos — but it is important to keep your eyes on the real goal: data contextualization and the extraction of valuable insights based on complex information inputs.
Another necessity is the creation of a touchless and contactless environment that utilizes intelligent process automation, chatbots, physical automation, automated workflows, AI-driven solutions based on image recognition, and augmented reality-based communication tools. Autonomous decision making by digital tools should be combined with human-driven risk identification and mitigation. This will lead to robust risk management — and more value as complex mitigation tasks are completed.
Organizations should seek business opportunities for physical products that have been enhanced digitally (e.g., services based on subscription leveraging of IoT, cloud-based platforms, AI-based technology, advanced analytics). Strive to become the orchestrator of an ecosystem-based service — and thus take control of the customer experience and business model.
However, even if you improve the flexibility and transparency of processes, supply chain irregularity can still be a major constraint. If you lack chips, you cannot do much about it.
Leverage a control tower to track, analyze, and contextualize supply chain data, manage collaborations, and orchestrate the supply chain ecosystem. Look behind beyond Tier 1 and Tier 2 suppliers and establish transparency for the entire chain. Unlock the power of blockchain! The need for detailed traceability has been significantly amplified during the pandemic.
Expand the supply chain into a supply network. On-demand digital manufacturing platforms deliver flexible sourcing without compromising quality or the on-time, in-full approach.
Sustainability should become part of company DNA. Digital technology enables improved water management, reduced carbon footprints, and compliance with green regulations. Seize the benefits of the circular economy for sustainable product design, green logistics, and reusable products.
Digital twin and digital thread technology provides organizations with detailed information on a product’s life cycle. This can make the product more environment-friendly while preserving its business attractiveness.
Despite gains in automation and autonomous environments, the human factor remains central to factory operations. Manufacturing organizations have adopted hybrid models that let relevant employees work from anywhere. The enabler: reliable and safe digital infrastructure.
Resiliency depends on a digitally capable workforce. The transformed organization requires a savvy C-level and middle management that understand benefits and costs and are also fluent in digital solutions.
Upskilling and reskilling are often touted, but the results are not unambiguous. Reskilling, for example, does not work for everybody (some workers do not have the requisite mental capacity). Reskilling initiatives, however, will be boosted by the increasing development of user-friendly digital interfaces that feature preprogrammed embedded functions.
Workforce transformation continues relentlessly. IDC predicts that in 2024, two-thirds of employees at high-performing G2000 enterprises will have shifted from static roles and processes to dynamic, multidisciplinary, outcome-focused, reconfigurable teams.
No doubt, the truly resilient manufacturing organization must be based on digital technology. Digital brings order to the complexity of processes and data. It builds trust across the ecosystem.
Critically, however, people must be ready to drive such significant change. More labor for machines — and more decision making and critical thinking for human brains!
Jan Burian, Senior Director, Head of IDC Manufacturing Insights EMEA and Leader of IDC Future of Operations Europe Practice